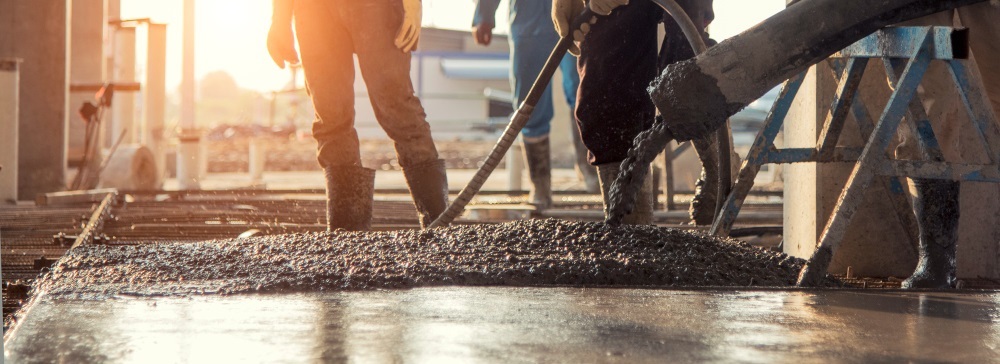
11 Types of Concrete Used in Construction Projects
Mar 19 2024
Concrete is a widely used building material all around the globe. It is used in almost all types of construction projects, from small residential homes to skyscrapers and bridges to tunnels. Concrete is the most durable and strong material because it does not burn, rust, or decay. In addition, it comes in different types and serves several purposes,
In this blog, Brick & Bolt provides all the basic information about concrete. So, let’s explore this core building material and learn the different types of concrete used in construction, including plain concrete, polymer concrete, reinforced concrete, fiber-reinforced concrete, ready-mix concrete, lightweight concrete, and self-compacting concrete.
Let’s start with, ‘what is concrete?’
What is Concrete?
Concrete is a mixture of cement, sand or fine aggregates, coarse aggregates, water, and admixtures. Cement, sand and coarse aggregates are the major raw materials for concrete, and they need to be precisely proportioned before making concrete to produce a mixture that is strong and long-lasting. Moreover, the proportions of each component added to concrete vary depending on the type of concrete being made, and the components react differently with each other based on this ratio. Workability, strength, durability, creep, shrinkage, etc., are the prime properties of concrete.
Now, let’s explore how many types of concrete are available for construction.
Different Types of Concrete Used in Construction
The following are the different types of concrete used in construction.
Normal Strength Concrete
Normal-strength concrete is made by combining the four basic materials - cement, sand, coarse aggregate and water. Its strength ranges from 10 MPa to 40 MPa, which depends on the characteristics of the cement you used and the local weather conditions at the construction site, and its initial setting time is 30 to 90 minutes.
Plain Concrete
A basic concrete mix called plain cement concrete or PCC, consists of cement, water, fine and coarse aggregates, and optional admixtures. PCC has excellent compression strength. However, it is extremely weak in tension because it lacks steel or other reinforcements. PCC mixes are typically designed with a 1:2:4 and 1:3:6 ratio. It is frequently used in the foundation of a building.
Reinforced Concrete
Reinforced concrete, also called reinforced cement concrete, is created using reinforced bars; typically, rebar is used to increase the tensile strength of the concrete. The overall durability of the concrete is increased when its compressive strength and the tensile strength of the reinforcement material are combined. It is mostly suitable for large-scale construction projects requiring high tensile strength, like tall buildings, bridges, dams, or any other structure where a structure must support incredibly heavy loads.
Lightweight Concrete
As the name suggests, lightweight concrete has a lower density, and it is used to decrease the structure's self-weight. Lightweight aggregates like silica sand, pumice, sawdust, scoria, and volcanic cinder blocks are used to make lightweight concrete. Any type of concrete with a density level of less than 1920 kg/m3 is considered lightweight concrete because the specific aggregates selected are what ultimately determine the density of the finished product. Lightweight concrete is used for walls, flooring, and places where the overall "dead weight" of a building can be decreased to help prevent collapse.
Ready-Mix Concrete
Ready mix concrete is produced in a manufacturing plant and transported to a building site through a truck that is equipped with a mixer. To ensure that the cement is ready to pour at the job site without hardening beforehand, it typically contains admixtures.
Polymer Concrete
Polymer concrete is made by replacing a polymer binder that cures and hardens for the lime and shale-based Portland cement. Examples of polymer binder materials include polyester, epoxy mixtures, vinyl ester, acrylics, and many other types of polymer resins. The type of resin used in the concrete determines the goal of polymer concrete. For example, epoxy binders help reduce shrinkage during curing, while acrylic binders provide weather resistance and faster setting times. Because polymer plastic is more sticky than cement, it can be added to concrete to create a mix with a higher tensile strength than one made only of Portland cement. Because polymer concrete resists corrosion well, it is frequently used in sewer systems, swimming pools, and other constructions that come into direct contact with liquids and chemicals that can cause corrosion.
Glass Concrete
Glass concrete is one of the special types of concrete in civil engineering. When recycled glass is added to the concrete as an aggregate or, depending on the desired result, substituted for both fine and coarse aggregates, the mixture is referred to as glass concrete. Glass aggregates can range in size from a fine talc-like powder to gravel-side pieces to six-inch glass rocks, and they are almost always made from recycled glass. Depending on the desired appearance, glass can either be used in chunks when mixed with cement or crushed using a glass crushing machine. Glass concrete is a visually appealing and extremely polished-looking material for countertops, floors, and tiles because it usually has a shiny or "glowing" appearance.
Pervious Concrete
Pervious concrete is a porous concrete that allows water to seep through to groundwater below. Pervious concrete is used to construct pavements and roads. It can absorb water at a rate of up to five gallons per minute and is made to deal with stormwater accumulation. With little to no fine aggregates, this type of concrete has more space for air and water to flow through and due to that Stormwater can filter through the pervious concrete and seep into the earth.
Air-Entrained Concrete
Concrete with tiny air bubbles in it that aid in releasing internal pressure is known as air-entrained concrete. During the mixing process, an air-entraining agent is added, which lowers the surface tension and creates air pockets in the slurry. When there are freeze-thaw conditions- temperature swings from below to above freezing- this type of concrete is appropriate for building environments where there is a build-up of water. Over time, the structure will last longer because the tiny pockets give water room to expand, preventing concrete from cracking and resisting scaling. 5% to 7% of the concrete mix is made up of microscopic air bubbles. Because adding air to concrete reduces its density, more cement is used to compensate for the strength.
Self-Compacting Concrete
Self-compacting concrete, one of the special types of concrete in civil engineering, also known as self-consolidating concrete, is a type of concrete that possesses three special characteristics like,
A high filling ability that allows it to easily flow in all directions around confined spaces and obstacles like steel reinforcement when it is poured;
A high passing ability that allows it to pass around these obstacles;
Segregation resistance, or the ability to maintain its original state during transportation, placement, and after placement.
With less labour and a faster concrete placement time, these characteristics allow the concrete to set into the mould very closely without the need for additional support or vibration. Self-compacted concrete is more fluid because it contains more fine aggregate, typically sand, and additives like superplasticizers and viscosity-enhancing admixtures, which make sure the sand particles are evenly distributed. This kind of concrete is made by mixing these additives with the standard ingredients—cement, fine and coarse aggregate, and water—in a concrete mixer.
Fiber-Reinforced Concrete
A composite material consisting of cement, water, aggregates, and rounded or flat fibers is called fiber-reinforced concrete. Many fiber types, including carbon, asbestos, glass, steel, polypropylene, and organic fibers, are used widely for reducing permeability, bleeding, and the development of small cracks. Fiber-reinforced concrete is widely used in the construction of dams, roads, bridges, runways, walls, aircraft parking areas, pavements, etc.
Sounds interesting!
Don’t worry; Brick&Bolt has written a detailed blog on fiber-reinforced concrete. To read more, click on the link below:
Fiber-Reinforced Concrete: All You Need To Know
Hire the best house construction service
4500+
Homes
470+
Quality Checks
100%
Safe Money Transaction