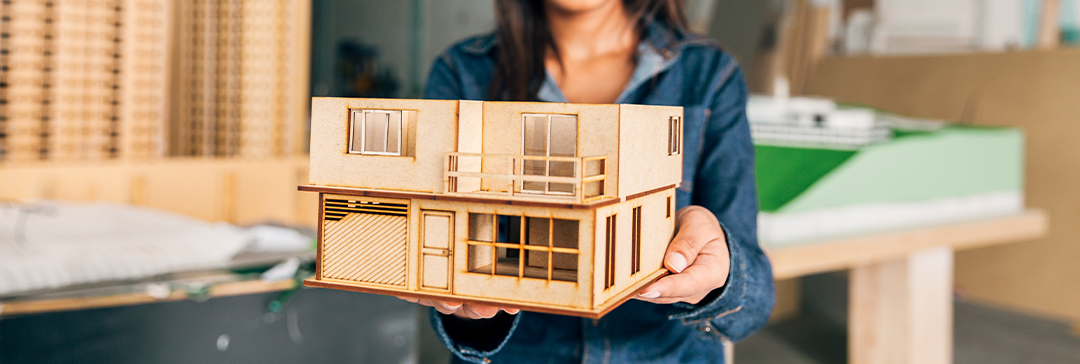
Benefits of Modular and Prefabricated Construction
Mar 13 2024
The advent of prefabricated and modular buildings has brought about a fundamental change in the construction paradigm. These techniques change the building industry by providing advantages like shorter construction times, cost-effectiveness, improved quality control, sustainability, and design flexibility. The potential of modular construction has been effectively increased by renowned projects worldwide. Modular and prefabricated construction will shape future cities and communities to a greater extent as technology develops and the need for sustainable and efficient building increases. In this blog, Brick & Bolt provides detailed information about the benefits of modular and prefabricated construction, helping you understand how these cutting-edge methods are transforming the construction industry from cost-effectiveness to speedy project completion. Prefabricated and modular construction differs from traditional on-site building because the components are produced off-site in controlled manufacturing facilities. Then, these modules or components are delivered to the building site, where they will be assembled. Modular and prefabricated building systems are becoming increasingly popular in the construction industry due to their numerous benefits. These techniques provide a comprehensive range of advantages, including reduced time and expenses and enhanced quality, sustainability, and safety. So, let’s explore all the benefits of modular and prefabricated construction in detail: One of the primary advantages of prefabricated and modular buildings is the significant reduction of project timelines. Unlike traditional construction, which requires finishing various on-site tasks in sequence, modular construction permits simultaneous fabrication of building components off-site and on-site preparation. This parallel approach is preferred for projects with tight deadlines because of its significant speed boost. Prefabricated and modular buildings can result in cost reductions in several ways. The regulated environment of off-site manufacturing minimizes material waste, and mass-producing standardized components leads to economies of scale. Additionally, the method is financially appealing to construction companies and builders due to its capacity to reduce the number of on-site workers required and shorten building timelines, improving overall cost efficiency. The regulated environment of the factory-based construction sector makes strict quality control measures feasible. Every building module or component is carefully inspected to meet all requirements as per specifications. Because of this dedication to quality, mistakes and irregularities are reduced, resulting in structures with improved overall construction quality, longevity, and reliability. Green building approaches are aligned with modular and prefabricated construction in an era where sustainability is a critical factor. Waste is reduced by optimised material consumption in the regulated manufacturing process. Effective resource management also facilitates reducing environmental impact in a production context. The ecological impact of modular construction is further reduced by using sustainable materials and recycled or repurposed components. When modular construction is used, architects and designers have great creative freedom. Numerous design options can be produced by combining various configurations of standardised construction components. Projects that require unusual or distinctive building structures benefit from this flexibility. Prefabricated and modular buildings can reduce the amount of on-site disturbance that occurs while a project is being built. Most of the building assembly is completed off-site, simplifying on-site operations and reducing noise pollution in the neighbourhood. This is particularly crucial in crowded urban locations where conventional construction techniques can be inconvenient. Conventional building projects frequently experience delays and higher costs due to weather-related factors. Because modular construction is mainly done in a controlled manufacturing setting, weather-related disruptions are less likely to occur. Due to its weather independence, building timelines are more predictable, and project delays have less potential. One of the main concerns in the building is safety. Workers have a safer working environment in a factory setting because of the controlled environment, which lowers the dangers involved with on-site construction tasks. Better planning and implementation of safety measures can also result from modular building approaches and standardised components. What is Modular and Prefabricated Construction?
Benefits of Modular and Prefabricated Construction
Reduced Construction Time
Cost-Effectiveness
Quality Control
Sustainability
Flexibility and Design Innovation
Minimised On-Site Disruption
Weather Independence
Improved Safety
Conclusion
In conclusion, prefabricated and modular construction provides a compelling future for the building industry by constructing a faster, wiser, and healthier future. These innovative ideas imagine a future where project completion times are shortened, costs are reduced, and environmental impact is minimized, all thanks to prioritising efficiency, sustainability, and quality. With the advancement of technology and the growing demand for affordable, eco-friendly building solutions, modular and prefabricated construction is anticipated to play a significant role in shaping the future of our towns and cities.
Hire the best house construction service
4500+
Homes
470+
Quality Checks
100%
Safe Money Transaction