Most people planning to construct their homes are unfamiliar with the materials used in construction. Although it is optional to know all the details of the materials used for constructing the house, the knowledge of some major components used in building construction helps to make smart and budget-friendly choices.
Reinforced Cement Concrete (RCC) is one of the most commonly used terms related to building construction. It is a composite material made of concrete and steel reinforcement. To better understand the importance of RCC in the construction process, we have answered below some of the frequently asked questions regarding the use of RCC.
What is RCC in Construction?
Reinforced Cement Concrete (RCC) is a composite material made by hardening a mixture of cement, sand, gravel, and water. The properties of concrete differ to a broader extent depending upon the quality and proportion used in the mixture. Concrete can resist compression very well but becomes very weak when resisting tension. The solution to making the concrete strong is to add steel to the combination because steel has high tensile and bond strength compared to other materials. Therefore, the bond between steel and concrete becomes strong, and we can place steel bars at the tensile zones of the structures. This procedure is known as steel reinforcement, and after the reinforcement is completed, the mixture is called Reinforced Cement Concrete.
What are the main properties of RCC?
The important properties of RCC are as follows:
- It must have the ability to withstand adequate tensile strength, compressive strength, bending, and shear forces.
- The concrete must not show excessive deflection and spoil serviceability requirement
- The reinforcement needs to have a good covering so that corrosion does not occur
- The hair cracks that are formed should be within the permissible limit
- It should be good fire and weather-resistant
- The concrete can be molded into any desired shape and size while it is still fresh
- It should be a high-durability material
- Any load can be constructed to be supported by an RCC structure
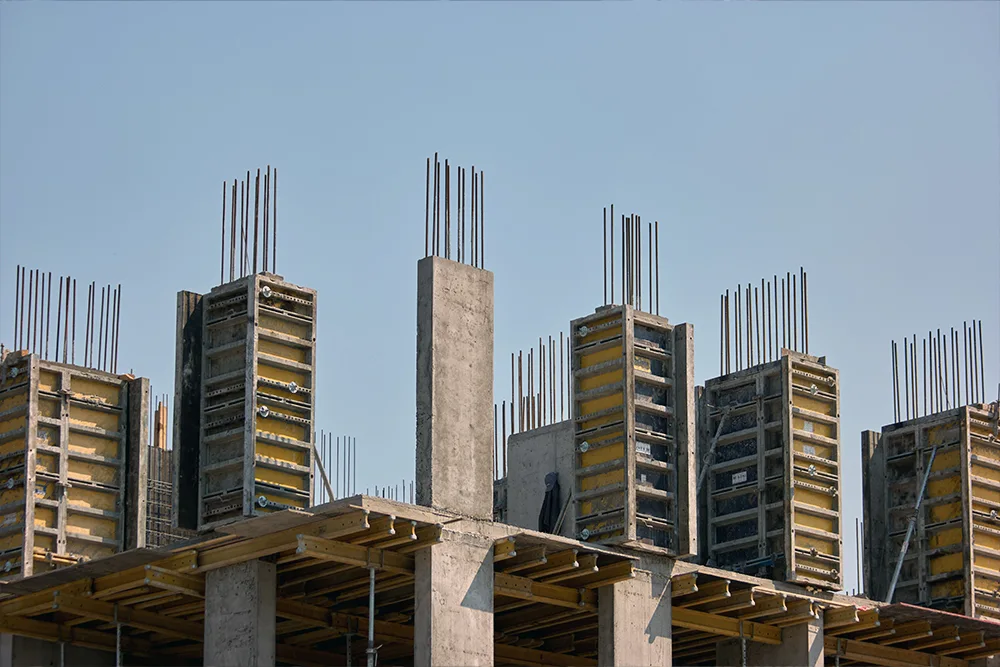
What are the advantages of using RCC in building construction?
Comparatively speaking, there are innumerable advantages of RCC in building construction. Let’s check some of them below:
- Reinforced concrete outperforms other building materials in terms of compressive and tensile strength
- RCC can withstand extremely high temperatures from fire for a longer period without losing structural integrity
- Buildings constructed with cast-in-place reinforced concrete can withstand winds of more than 200 miles per hour and also performs well even under the impact of flying debris
- Concrete performs effectively through both natural and man-made disasters and doesn’t need any additional fireproofing treatments to meet stringent fire codes
- When it comes to durability, RCC buildings are more resilient than other structures
- RCC structures are more durable and require less maintenance cost
- RCC buildings have more resistance to fire than just steel structures
- Compared to the construction of steel structures, the construction of RCC buildings requires less skilled people
What are the disadvantages of using RCC in building construction?
There are not many disadvantages of RCC in building construction, but a few are to be mentioned below:
- Only around one-tenth of reinforced concrete’s compressive strength is available as tensile strength
- Constructing an RCC building requires several steps, such as mixing, casting, and curing. If any of these steps are missed or not done correctly, the final strength of the RCC might change
- Compaction needs to be done correctly and in the right amount. Less vibration means less compaction, which means fewer strengths. Concrete segregation and bleeding are caused by heavy vibration
- Shrinkage in RCC buildings after hardening may result in crack development and strength loss
What are the different types of reinforcement used in RCC Concrete?
There are mainly four types of steel reinforcement that are used in concrete structures during construction:
Hot Rolled Deformed Bars:
For conventional RCC constructions, this method of reinforcement is the most typical. In the mills, hot rolling is carried out, which involves deformations on the surface, i.e., ribs, which helps to create a bond with the concrete. The stress-strain curve has a clear yield point, followed by a plastic stage in which the strain increases without an increase in stress.
Cold Twisted Deformed Bars:
Cold-worked reinforcement is created when a hot rolled steel bar undergoes the process of cold working. The cold working method involves twisting or drawing the bars at room temperature. Though it allows more control over bar size and tolerances, this basically eliminates the Plastic Stage from the Stress-Strain curve. Due to the removal of the plastic stage, these bars have lower ductility than hot Rolled bars. The usage of these kinds of bars is specific to projects where low tolerances and straightness are an important concern.
TMT Bars:
TMT stands for Thermo-mechanically Treated Reinforcement Bars. These bars are produced by sudden quenching of red hot steel bars with a water spray and can produce steel bars with high strength at the surface with a core of mild steel. To improve the bond strength of the bars, TMT bars are also produced with ribs (rebars). Adding corrosion-resistant materials like copper, phosphorus, and chromium gives TMT bars their corrosion resistance feature.
TMT bars are more corrosion-resistant than Tor Steel and are strongly advised for usage in reinforced concrete projects. Fe 415, Fe 500, Fe 550, and Fe 600 are the four grades in which these TMT bars are manufactured.
Prestressing Steel Bars:
It is used in the form of bars or tendons that are usually made up of multiple strands. However, these tendons/strands are more frequently used because these can be laid in various profiles, which is a primary requirement of prestressing steel. Prestressing strands are composed of several wires (typically 2, 3, or 7 wire strands). These wires are primarily cold-drawn and have high tensile ultimate strength, which is helpful for construction purposes.
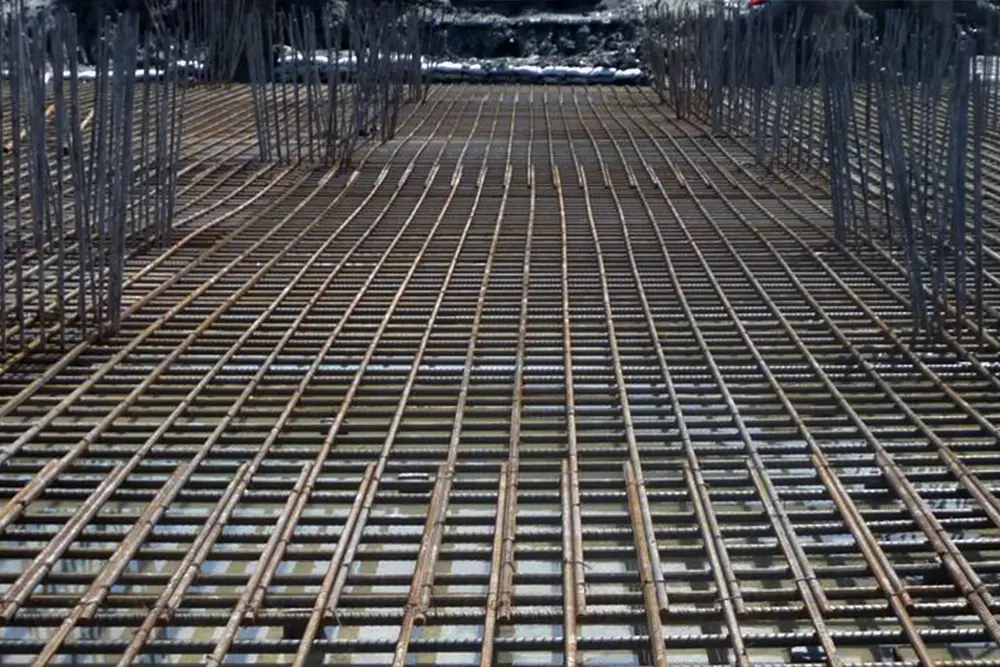
Is RCC better or PCC?
Technically, RCC is stronger than PCC in terms of strength as the reinforcement helps in load-carrying capacity. PCC is weaker and is only used to layer surfaces, such as flooring or plastering, and, most significantly, to layer excavation to cast footings.
Due to its ability to withstand high stress and large loads, RCC is used in most civil construction projects.
What is the ratio for RCC used during construction?
In the home, the most popular and safest concrete mix ratio used for RCC column construction is 1: 1: 2 (cement, sand, and aggregate), in which one part is cement, one part is sand, and two parts are aggregate. For RCC column construction, a concrete mix ratio of 1: 1.5: 3 or 1: 1: 2 (cement, sand, and aggregate) is typically used.
What do you mean by RCC slab?
A reinforced concrete slab also referred to as an “RCC Slab,” is one of the most important parts of a building. It is a structural component of modern buildings. Beams and columns hold up slabs.
The most popular RCC Slabs for building floors and ceilings range in thickness from 10 to 50 centimeters. Additionally, thin concrete slabs are employed for paving outside surfaces.
The ground floor of a building is often constructed of a thick concrete slab that is supported by foundations or directly on the subsoil in many houses and industrial structures. Thinner, pre-cast concrete slabs are stretched between the steel frames to create the floors and ceilings on each level of high-rise buildings and skyscrapers.
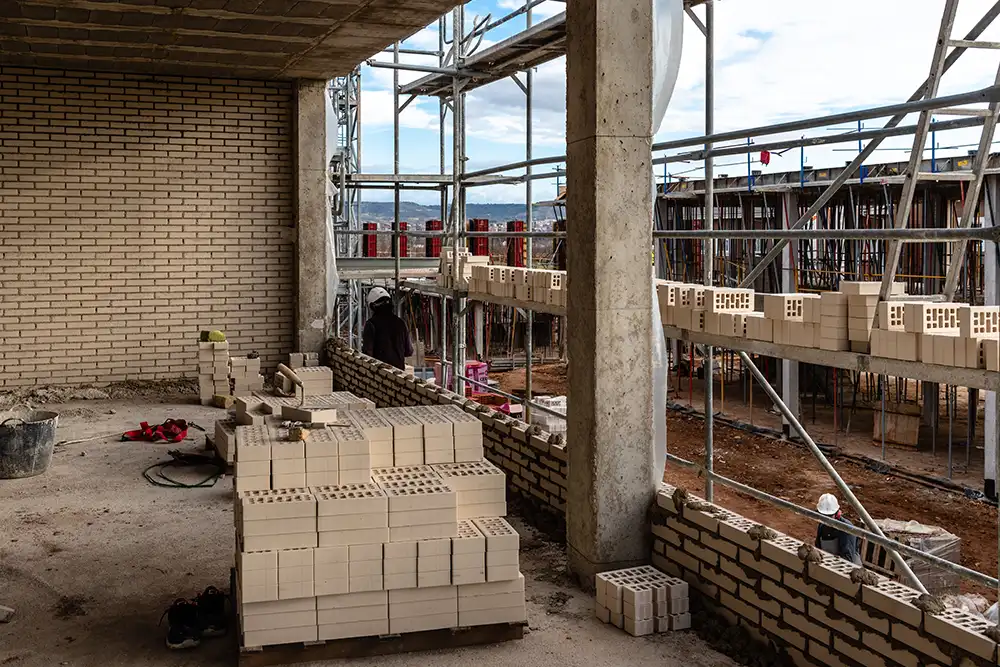
What are the different types of slabs?
Five types of slabs are generally used for the construction of a building:
Corrugated Slab:
Concrete is poured into a corrugated steel tray to create this kind of slab. With this kind of RCC slab, the strength is increased, and the slabs won’t bend under their own weight. This slab runs across from side to side.
1) A Ribbed Slab:
This slab category provides extra strength in one direction.
2) A Waffle Slab:
Additional strength is provided in both directions by this kind of slab
3) One-way Slab:
This type of slab has structural strength in the shortest direction
4) Two-way Slab:
This type of slab has structural strength in two directions
What is meant by Curing?
Curing is the process of keeping concrete at an appropriate temperature and moisture level at an early age to develop the properties of the mixture that it was intended to achieve. After finishing and placing, the concrete must cure for it to acquire the appropriate durability and strength. With sufficient moisture, the cementitious materials of concrete can react to produce a high-quality final product.
Curing thus concludes the RCC slab casting process.
We hope we could answer most of your queries regarding RCC in building construction. If you still have any questions or need to get a free quote, connect with Brick&Bolt, India’s best construction company in India