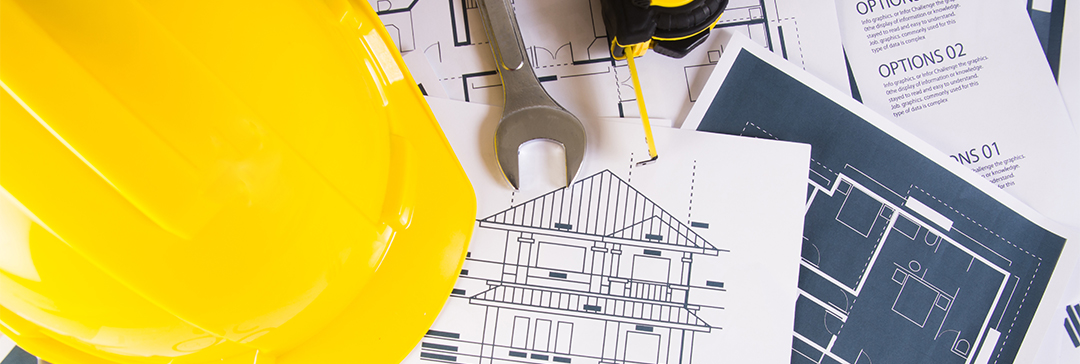
How Modular Building Methods Expedite Construction Timelines
Feb 20 2024
Modular construction is increasingly becoming the preferred choice for developers aiming to expedite building timelines. By employing prefabricated modules, modern modular construction methods significantly reduce the need for extensive onsite labour and mitigate the risks associated with scheduling uncertainties due to weather conditions or coordination challenges among contractors. Creating a modular construction structure involves producing standard building components, or modules, offsite and then transporting them to the construction site for quick assembly into the finished product. The same components and architectural layouts used in traditional buildings are used to construct modules in a quality-controlled facility. Both separately and when assembled the module's structural stability allows for future extensions. The following are some significant distinctions between conventional and modular construction techniques: Location: Offsite modular components versus on-site stick-built Materials: A few transport-related design restrictions but a wide range of alternatives Timeline: Timetable Concurrent construction of modules and site work allows for speedier projects. Customisation: Customisation is possible thanks to manufacturing techniques. Quality Control: Optimal facility conditions allow for exceptional quality guarantee The final building supplied may differ slightly in terms of functionality. However, the modular approach minimises onsite waste, embeds quality, and speeds up timelines. Project Timeline Reduction by 30-50%: Offsite fabrication significantly speeds up construction. Year-round Construction Without Weather Interruptions: The indoor factory environment allows continuous operation. Superior Quality Assurance: The standardisation of modular units ensures consistent quality. Improved Safety:Fabricating modules at ground level minimises the risks associated with high-altitude work. Enhanced Cost Predictability:With 60-90% of the construction completed offsite, financial uncertainties are greatly reduced. Flexibility for Relocation: Modular units can be disassembled and relocated as needed. Modular construction is particularly advantageous for certain types of projects, including: Hotels and hospitality facilities with strict budget constraints Multi-unit residential structures, such as apartments or dormitories Educational spaces, healthcare facilities, and emergency housing Temporary offices and pilot projects with potential future relocation Construction projects in remote locations with limited access to skilled labor The following are some essential strategies for creating excellent modular building components: To facilitate effective onsite assembly, use interlocking connections between modules. To provide flexibility, standardise module sizes. Create modules that are easily transportable without sacrificing structural soundness. Connections between modules must line up exactly Site variability must be taken into consideration; modifications must be tolerated. Facade interfaces should minimise complex site assemblies. When creating modules, pay great attention to construction codes and transportation requirements. Collaborate closely with manufacturers and contractors. Lean manufacturing reduces waste. Automation and robotics enable customisation, and repeatability of industrial conditions assures quality. To maximise loads, take into account module size divisions. Draw safe routes for hauling with enough room for turns. Module details to guard against damage during transit Subassemblies made out of standardised parts streamline production Repetitive design components increase efficiency and lower costs. Across modules, coordinate the design of the plumbing, electrical, and HVAC systems. Hold key systems in separate modules that are ready for the plant. The construction world is beginning to realise how much modular construction can do to improve quality, cost, and efficiency in various project types. Modular construction is expected to be more effective and efficient than traditional building techniques, offering the prospect of quicker completion timeframes and more regulated production processes. The construction industry is transitioning tremendously due to advancements in prefabrication technologies and modular procedures. Offsite building procedures are changing the face of both commercial and residential development, signalling a shift toward more environmentally friendly, productive, and flexible building techniques. Companies like Brick&Bolt are leading the way in the modular construction revolution as the construction sector develops further. Brick&Bolt is a company that personifies the creative spirit of modular construction. They provide clients with greater cost predictability, quicker project schedules, and enhanced quality control. Their dedication to utilising prefabrication methods places them in a pivotal role in revolutionising conventional construction methodologies. The modular building strategy used by Brick & Bolt illustrates the useful benefits of this approach as well as the company's contribution to advancing the sector's transition to a more efficient and sustainable future. By utilising modular construction, Brick&Bolt is creating more than simply buildings rather, they are establishing a reputation for excellence, innovation, and quality in the building sector. In summary, modular construction is the way of the future for building due to its many uses and advantages. Leading the way are businesses like Brick&Bolt, which demonstrate that construction processes can be greatly shortened without sacrificing sustainability or quality with the appropriate strategy. Modular buildings and pioneers like Brick&Bolt will be crucial in influencing the built environment of the future as we look to the future.Exploring Modular Construction in the Prefabrication Age
Differences Between Modular and Conventional Buildings
Benefits of Modular Prefabricated Construction Techniques
Adopting modular construction offers numerous benefits over traditional construction methods, notable for:
Appropriate Applications for Modular Construction
Key Strategies for Successful Modular Building Components
1. Design for Manufacturing and Assembly (DfMA):
2. Pay Attention to Interface Details:
3. Organize the Needs for Design
4. Make Use of Precision Manufacturing Capabilities
5. Make an Effective Transportation Plan
6. Wherever Possible, Standardised
7. Take Care of Building Services
The Prospective Landscape of Offsite Modular Fabrication
Hire the best house construction service
4500+
Homes
470+
Quality Checks
100%
Safe Money Transaction